PNP-NPN-Input-Output-Potential-free-interface-with-industrial-robot:
The I/O on UR masterboard inside the controller are PNP type.
However there are two NPN outputs on the UR – which are the 2 output on the tool head that are NPN – the rest inside the main controller cabinet are PNP.
If NPN is desired then this can be acheived by adding MODBUS nodes e.g. Beckhoff external I/O nodes.
Below are two logic diagrams to illustrate some of the differences.
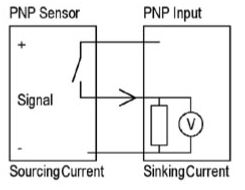
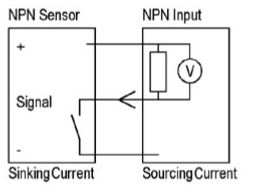
The type of PNP or NPN must fit together in order to interface correct – for example if a input is a PNP input then the component (maybe a photo sensor) also must be a PNP type. It is possible with some transistor logic to make a PNP component behave as a NPN component and soem modern components has selector switch for the type.
Digital Outputs on tool head are Open collector type. Open collector means that the outputs are implemented to ”sink” and we can say they are ”Active low” because connecting an actuator can be done by applying the supply voltage at the ”far” end of the actuator connections and the other connection to the output terminal – and then when the output is driven low by the programmer – the external device turns on.
If you prefer to have an ”Active high” output – it is also possible – then just apply a ”pull up resistor”. So now the ”far” end of the external device is connected to GND and the other end is connected to the output and a pull up resistor. The pull up resistor is connected to the supply voltage. Now when the output is driven ”high” by the programmer the external device turns on.
Open collector is actually an advantage because it gives the implementation more choices.
Potential Free Interface with external components:
If two control systems needs to interface and be connected togeteher for example two PLC systems or a PLC and a Universal-Robots – then a potential free interfaces are desired because then the power systems on each of the two connecting control systems are not mixed together. Sometimes the connecting components are not the same power level and by using a potential free methods then such components can still interface.
Potential free can just mean that and output when activated just close a contact set(for example by a relay with contact set). Then the corresponding input on the device interfaced with (e.g. a PLC or an input on the UR) power (12V or 24V DC) are connected to one side of the contact and the other side of the contact is connected to the input. This means that when the output is activated – then it is the inputs own power source that is lead back to the input and therefore the power on the output side is not connected to the input side at all.
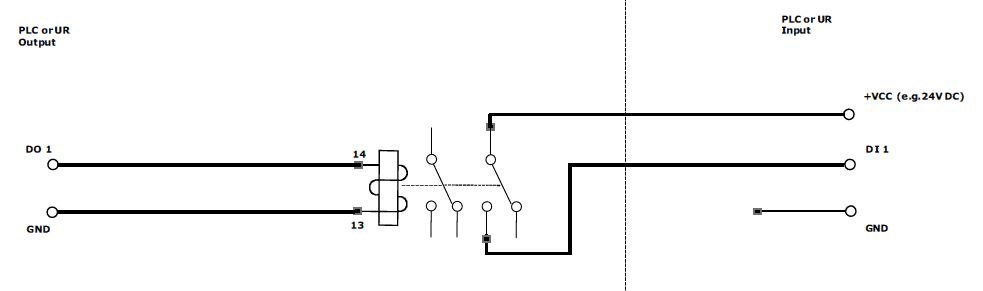
In this illustration the output activates a relay that closes a contact set. The input side Vcc is connected to one side of the contact terminals. When the contact closes the Vcc is lead to the input.
In this method there is no mix of power from side to side and thereby it is a potential free interface.
The method of “Potential Free” signal exchange is more elegant because then one machine can be 12 Volt and the other can be 24 volt – the input is feed through the contact on the other side by the same power source as the input itself.
This principle of Potential Free handshake is better to use for signal interface for example if the start signal from a CNC machine is a dry contact controlled by a relay on an output on the CNC machine – and then the input on the robot is connected to the contact. That’s “Potential Free” signal exchange and the Power Supplies on the two machines is not connected together and the handshake is through the dry contacts.
Disclaimer: While the Zacobria Pte. Ltd. believes that information and guidance provided is correct, parties must rely upon their skill and judgement when making use of them. Zacobria Pte. Ltd. assumes no liability for loss or damage caused by error or omission, whether such an error or omission is the result of negligence or any other cause. Where reference is made to legislation it is not to be considered as legal advice. Any and all such liability is disclaimed.
If you need specific advice (for example, medical, legal, financial or risk management), please seek a professional who is licensed or knowledgeable in that area.
Author:
By Zacobria Lars Skovsgaard
Accredited 2015-2018 Universal Robots support Centre and Forum.